工業製品の初期ロットは買うな。製品開発プロセスから理由を説明。
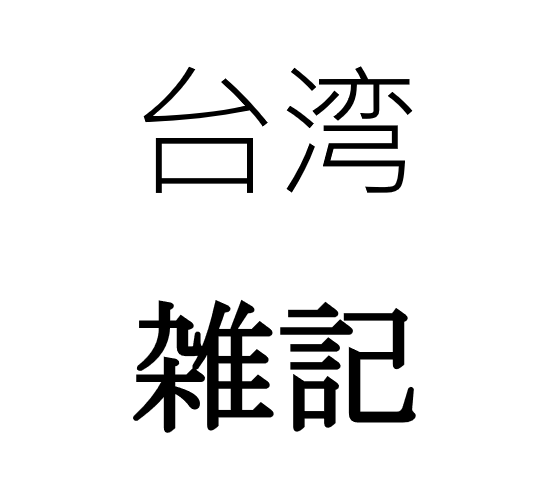
どーもこんにちは。
台風が心配な台湾マスターです。
さて、今回は製造業(モノづくり)に関係する記事を書こうと思います。
この記事も見てください。
私たちの周りには様々な工業製品がありますね。少し今あなたの周りにあるモノを見てみてください。
今この記事を見ていただいている方なら、その手にはスマホがあります。パソコンで見ている方もいることでしょう。タブレットで見てる方もいると思います。
これらすべて工業製品ですね。
お子さんがおられる家庭ならオモチャや、ゲームが家にあります。これも工業製品です。
掃除機、レンジ、冷蔵庫、テレビ等の家電もそうです。
実際、身の回りにあるものすべてが工業製品に支配されているといっても過言ではないでしょう。
そんな中、声を大にして言いたいこと。それは
工業製品の初期ロットは買うな。
です。
新製品が出るとすぐに手に入れたいと思いますよね。iPhoneやMacなどのアップル製品の新機種が出るたびにアップルストアには行列ができます。ゲーム機もそうですよね。新しいゲーム機がでると、なかなか手に入りません。ニンテンドーSwitchがいい例です。
でも、ツウは発売したての初期ロット製品は買いません。
故障や不具合発生のリスクが高すぎるからです。
なぜ初期ロット品を避けるべきなのでしょうかね?
製品開発プロセスからその理由を探ってみましょう。
※工業製品の初期ロットは買わない方がいい理由のみを知りたい人は、下の開発プロセスのくだりは飛ばして読んでくださいね。
製品開発プロセス
製品開発プロセスは企業により手法や呼び方が異なります。ここでは一般的な新製品開発の流れを説明します。
基本的に、開発プロセスは以下となっております。
企画
↓
構想設計
↓
モックアップ:ES(Engineering Sample)
↓
試作:TP(Trial-Production)
↓
量産試作:PP(Pre-Production)
↓
量産:MP(Mass-Production)
↓
出荷&販売
企画
マーケティング部門はこの段階で
市場で今どんな製品が売れているのか?
将来的に売れそうな製品は何か?
について徹底的に調査します。調査会社に市場調査を依頼したり、自社の営業部門の聞き取り調査を実施したり、販売店や代理店に出向き、意見を聞いてみたり、見本市や展示会に出向き国内・海外のトレンドを調査することもあります。
その後、企業としてどのような製品を世に送り出すかを意思決定します。
ハイエンドなのかミドルレンジなのかローエンドなのか?
について、製品のターゲットプライス(目標価格)を設定し、次に外観デザインに着手します。概略のデザインが終われば、その情報を技術開発グループ伝達します。
構想設計
マーケティング部門と技術開発部門とが話し合い、製品コンセプトやデザインをもとに設計内容を具現化していきます。
どのような材質を使用するか、部品に何をつかうか、スペックをどうするか等について徹底的に話し合い決定します。
企業によっては品質保証部門もこの段階から参加し、過去に開発されたの類似製品の問題点等について助言します。
モックアップ:ES(Engineering Sample)
構想設計が終われば、モックアップを作ります。モックアップとは原寸大の模型です。例えばケータイショップにおいてあるような形と重量が本物と一緒で、それ以外にはなんの機能もないスマホがありますが、あれもモックアップの一種です。
モックアップ品は基本的には外観の確認のために使用するものなので、内部には部品等が実装されていません。
このモックアップ品を製作する段階を業界では
ES(Enginering Sample:エンジニアリングサンプル)
と呼んでいます。
モックアップ作製は時間もお金もかかる作業ですが、モノづくりにおいては非常に重要なステップです。図面だけで確認するのと、実際の「モノ」で確認するのとではえらい違いですからね。
以前まではモックアップ品は社内で作らず、概略図面が出来上がった段階で外注業者に作製を依頼する場合が多くかったため、モックアップ製作に特化した業者がたくさんいました。
詳細寸法が記載されていない簡単なデザイン図をもとに、モックアップ品を作ってくれるすごい業者もいました。
しかし、最近このような業者も減ってきています。なぜだかわかりますか?
3Dプリンターが登場したからです。
高いお金を払って外注業者に依頼せずとも、自社で3Dプリンターを購入すれば簡単にモックアップを作れるようになったからです。
もちろん家庭用の安い3Dプリンターなどでは話になりませんが、1,000万円ほどの3Dプリンターであれば、非常に精密な、量産品に近いモックアップを作製する事が可能になったのです。
しかも図面さえ出来上がっていればものすごいスピードで作製が可能です。3Dプリンターがない時代では3週間ほどかかっていた作業も、今では1日、2日あれば外観パーツを作製し組み立てることが可能になりました。ものすごいイノベーションです。
もちろん3Dプリンターを導入していない企業であればモックアップ業者に依頼せざるを得ないでしょう。しかし値は張りますが自社で3Dプリンターを購入し設備投資した方が圧倒的に開発効率がいいです。また、開発コストの観点から言っても、長期的に見れば3Dプリンターを購入した方が安くつきます。
上記理由で、今モックアップ業者は大打撃を受けています。
話が少し脱線してしまいましたが、ESは非常に大事なステップです。
試作:TP(Trial-Production/Test-Production)
ESが終われば次はいよいよ金型を起工し、試作の段階へと進みます。
企業により呼び方は異なりますが、
TP(Trial-Production/Test-Production)
と呼ばれたりします。TPの段階からは基本的に品質保証部門主導にて製品開発が進められていきます。20台~50台ほど試作されます。
※EVT(Engineer verification test:技術検証段階) とかDVT(Design verification test:設計検証段階)とかPVT(Process verification Test:生産検証段階) に細かく分けている企業もあります。
各パーツの金型を起工し、出来上がったパーツと図面をチェックし、パーツ寸法・精度を確認し、同時にパーツ同士の嵌合(かんごう)を検証します。
もし問題が出れば、図面通りの寸法になるように金型修正を実施するか、あるいは図面修正を行い、図面を現物に合わせるような対応をとります。
パーツの確認が終わると、生産ラインにて組み立て作業を行い、「完成品」となります。
そして大事なポイントですが、
多くの企業がこの段階で信頼性試験と呼ばれる製品のテストを実施します。
製品に欠陥はないか?製品はユーザーの使用に耐えうるか?製品はスペックは満たしているか?等のモノづくりにおいて一番大事なテスト作業をこの段階で実施することになります。
もし問題が出れば、試作やり直しということで、TP2を実施し、それでも改善できなければTP3を実施したりして、徹底的に問題を洗い出し、そして問題をつぶしていきます。
量産試作:PP(Pre-Production)
試作(TP)が終了し、信頼性試験をPASSしたならば、次は量産試作となります。
業界では
PP(Pre-Production)
と呼ばれています。50台~100台ほど生産されます。
TPの段階では品質保証や技術担当者が生産ラインに入ってライン作業者に指導しつつ完成品まで組み立てる作業を実施しますが、PPとなると、作業はすべて生産ラインの作業者に任せて実施します。量産試作なので量産と同じ条件、同じ作業・検査手順で生産されます。
完成品が出来上がれば、量産時と同様の形態で梱包されそして出荷検査を受けます。
この間、各工程での作業時間が計られ、正確な工数を算出します。
梱包が終わった完成品は、自社の各部門や得意先に展示品サンプルとして出荷されます。家電量販店等の店頭で見るそして触れる新製品はこのPPのステップで作られた製品である場合が多いです。
量産:MP(Mass-Production)
この段階まで進めば、すべての作業がルーチン化され、技術や品質保証部門の監督なしに、すべてが現場のライン作業者によって行われます。
PDCA(Plan:計画・Do:実行・Check:評価・Action:改善)
のサイクルを回し、徹底的に作業の効率化を図るのもこの段階です。
出荷&販売
量産された製品は全国各地及び海外に出荷され、店頭で販売されます。
これで一先ず、開発プロセスが終了となります。
製品化までの期間
モノにもよりますが、一般的な家電製品の場合、上記開発プロセスに則って新製品が発売されるまでに1年~1年半の期間を要します。自動車などの複雑な工業製品ともなれば3年~5年はかかるでしょうし、飛行機であれば5年~10年はかかりますね。構造の簡単な家電製品であったり、既存の金型を流用するような製品であれば3ヵ月~半年で商品化へとこぎつける場合もありますが、一般的には1年~1年半が妥当です。
ではここで本題に入ります。
工業製品の初期ロットは買うな
初期ロットはファーストロットとも呼ばれ、量産後間もない出来立てホヤホヤの新製品の事です。
現在ほぼすべての工場ではロット管理を導入しているため、生産ロットを区切って製品を量産しています。
工場側で一番初めに買った(納入した)部品を使用し、初めて完成品まで組み立てられた量産品が初期ロット品です。
なぜ初期ロット品を買ったらだめなのか、その理由はずばり
故障やその他不具合が発生する可能性が極めて高いからです。
なぜそうなるかというと、3つ理由があります。
1.開発段階では量産後に発生するかもしれない不具合を予測できない。
2.初期ロット品の部品品質にバラツキがあり安定していない。
3.製品品質が担保されぬまま出荷される。
一つ一つ見ていきましょう。
開発段階では量産後に発生するかもしれない不具合を予測できない
試作の段階で信頼性試験等の各種テストを実施しますが、試作では多くても50台程しか作らないため、技術サンプルや顧客サンプルを引いた、20台~30台しか信頼性試験ができません。
もちろんメーカーにも蓄積したノウハウがありますから、ある程度の問題や瑕疵はこの少ない台数で洗い出し、解決することができます。しかし量産後、大量に製品が市場に出回った後に発生するかもしれない不具合を全部予測することは非常に困難です。
特に製品の耐久性等の問題は、通り一遍の信頼性試験では見つけることができず、量産後、製品が市場に出回ってから一定の期間が経った後に初めて顕在化します。ユーザーの使用環境や使い方は人によってだいぶ異なりますからね。機械的な試験では出ないような不具合も、人がある程度の期間実際に使用してから発覚するということがよくあります。
代表的なものとしては2010年に発売されたiPhone4で発生した電波受信障害の不具合。内蔵アンテナの位置の関係で握り方によっては受信感度が鈍るということが大問題になりましたね。
当時はバンパーを無料で配って対応するなどしていましたが、9月30日以降は配らなくなり、バンパーは有料となりましたね。不具合箇所にすぐ対策を実施し問題を修正したからだと考えられます。ソフトウェアでは改善できない問題だったので、発覚後すぐに内部設計を変更し対策したんでしょう。
通り一遍の信頼性試験の段階では発覚せずに、量産後はじめてわかった不具合ということで、初期ロットを買った人は残念な思いをしたはずです。
初期ロット品の部品にバラツキがあり安定していない
完成品まで組み立てるのはメーカーですが、メーカーはその部品のほとんどを外部の業者(部品ベンダー)から購入しています。
試作の段階でメーカーから部品の図面が届き、その図面に基づき、業者は金型を起こし部品を製作します。出来上がれば部品をメーカーに納品しますが、その部品の性能や寸法にNGが出れば、金型を修正したりして改めて部品をメーカーに納品します。場合によってはNGが連続し、この行ったり来たりの作業が5回、6回と続きます。
きちんと管理できている業者なら問題ないですが、管理ができていない業者になると旧仕様と新仕様が混ざって納品されたりする悲劇が発生します。
また、試作の段階で、量産仕様がやっとのことで確定したにも関わらず、いざ量産用の部品納入の際には、どれが最新仕様の部品かを忘れて、旧仕様の部品を納品してきたりするダメダメ業者もいます。
こういう状況なので、初期ロット品の部品品質にバラツキが生じ、安定しないという問題がたびたび発生します。
製品品質が担保されぬまま出荷される
なぜこんなことが起こるのでしょうか?それは、
開発期間が不足し、十分に検証できないまま出荷せざるを得ないケースが発生するからです。
前述の通り、製品開発には1年から1年半の時間が必要です。で、構想設計の段階でこの開発期間が加味された製品の量産スケジュールが決定し、発売時期も決まります。
そのあとはこのスケジュールに追われながら製品開発を進めることになります。
順調に開発が進めば問題ないですが、試作段階の信頼性試験等で問題が発生し、設計変更が必要になってくると、量産スケジュールに大きな影響が出ます。
試作(TP)で問題が発覚せず、量産試作(PP)の段階で発覚した場合はもう量産スケジュールが遅れる可能性大です。
こうなると、営業部門からめちゃくちゃなプレッシャーがかかってきます。
日程が遅れる=取引先に謝罪=商機逸失=売上減少
と営業部門にとっては死活問題となりますから、毎日のように日程厳守(死守)するようにとの指示がきます。
そんな綱渡りの状態で量産スケジュールをこなさないといけないですから、十分に製品品質を検証する時間などありません。
また、生産ラインも急ピッチで生産するようになるため、生産が雑になったりします。
そのため、製品が使えない、製品安全の問題がある、あるいは法令や規格を満たしていない等の致命的な不具合ではない場合、初期ロット品に小さな不具合、例えば外観的な欠陥があっても
「特採(特別採用)」
として出荷される場合があります。
最近では神戸製鋼所、三菱マテリアルの子会社、東レでこの「特採」を悪用し社会問題となりましたね。
初期ロット品ではスケジュールの関係でこの「特採」措置が取られることが多々あるため、十分な製品品質が担保されぬまま出荷されてしまっている可能性があります。
以上の理由が初期ロット品を買ってはいけない理由となります。
終わりに
開発期間を十分にとり、完成度の高い製品に仕上げてきた新製品であれば、初期ロット品でも全く問題ないものとなりますし、実際にそういう工業製品も多いでしょう。
稀に発売スケジュール遅らせざるを得なくなった企業もあり、そういう企業のイメージはよくありませんが、私からするとかなり良心的な企業だと思います。
下手な製品をだすくらいなら、もっと完成度の高い製品を世に送り出したい、と考えている企業ですからね。もっとも、発売時期が遅れるような管理をしている点はいただけないですが。
一般的に製品が量産・販売され、市場に出回った後、カスタマーサービスから様々な不具合事象について品質保証部門にその情報フィードバックされ、よりよい製品となるよう対策を施していきます。
新製品の生産が安定しだすのが量産開始して約半年後、そして不具合への対策・修正が実施されるのが量産開始してから半年~1年後ですので、安定した不具合の無い製品を購入したいのであれば、製品発売後少なくとも半年以上経過したものを購入した方が絶対にいいです。
1年以上経過している製品についてはより安心して購入できると思います。
自動車にしても新発売の新車よりもモデル末期の新車の方が圧倒的に品質がいいという話も聞きますもんね。
皆さんも、もしいい製品が欲しいのであれば、
初期ロット品は絶対に買ってはダメですよ!
以上
台湾マスターでした。
この記事にも注目!
-
前の記事
ダメ。ゼッタイ。臭豆腐の歴史とにおいの原因、そして作り方について。 2018.05.21
-
次の記事
超おすすめマットレス「モットン」。海外駐在・留学時に是非。 2018.07.20
おっしゃる通りだと思います。
しかし、事、トヨタの自動車に限って言えば、発表から1年以内に買った方が良いという話を聞きました。
知り合いの自動車関係者からの又聞きなので真実かどうかは分かりませんが、
発表から1年も経つと、素人には分からないようなところはコストカットで、別物になっているという
内容です。
確かに、実車のインプレッション記事なんて、大体は新車発表の数ヶ月ですから、その後は、手抜きをて
も分からないところは、どんどんコストを減らして利益を最大化するなんて事が出来るならやりますよね。
石井様
コメント頂きまして誠にありがとうございます。
確かに新車発表後間もない車について、意図的あるいは必然的に品質的にピークの状態になっていることは十分考えられますね。特に自動車メーカーの場合、特にトヨタはサプライヤーに対して定期的に値下げ交渉をすることで有名ですから、値下げを受け入れざるを得ないサプライヤー側は品質レベルを落とす、というかオーバースペック気味の部品については適正スペックに変更しコストダウン等を図っている可能性があります。私がサプライヤー側の経営者なら値下げ要求が将来的にある可能性大の部品については、初期ロットの部品についてはオーバースペック気味に製作し、納入します。で、値下げ要求があればそのコストを十分に吸収できるように適正スペックに落とす(戻す)。言い換えると、例えば耐久性が必要な部品について自動車メーカー側の品質基準が10,000回以上クリアすること、というのであれば初期ロットの部品については実力値的に20,000回をクリアするようなものを製造し納品。その後、値下げ要求があれば10,000回の耐久性を確保するのみの部品に「ダウングレード」し納品すれば、製造コストは下がるがメーカーの品質基準はきっちりクリアできている部品を納品しているということになるので、メーカー側も文句は言えないですよね。ある意味Win-Winになるわけです。
そう考えると、モノづくりっていうのは奥深いですね。私は今も勉強中です。